How to Choose Between Manual and Automated Industrial Valves for Your System
Industrial valves play a crucial role in controlling the flow of liquids, gases, and other materials within various systems. From oil and gas plants to water treatment facilities and manufacturing operations, valves are an integral part of ensuring system performance and safety. One of the most important decisions in designing or maintaining an industrial system is choosing between manual and automated valves. Both types offer unique advantages and have specific use cases, but selecting the wrong one can lead to inefficiencies, increased operational costs, or even safety hazards.
This article will explore the key differences between manual and automated valves, the advantages and limitations of each, and how to make the best decision for your system based on your industry’s needs and operational requirements.
What Are Manual Industrial Valves?
Manual valves are operated by hand using levers, wheels, or handles to open, close, or regulate the flow of a material. These types of valves are simple, reliable, and have been used in industrial systems for decades. They offer a hands-on approach to flow control, requiring an operator to manually adjust them when necessary.
Do you want to visit Char Dham? Char Dham Travel Agent is the best place to plan your Char Dham tour. You can book the tour from here.
Types of Manual Valves Include:
- Gate Valves: Best for on/off control with minimal fluid resistance.
- Globe Valves: Designed for throttling flow and more precise control.
- Butterfly Valves: Used for quick shutoff in large systems.
- Ball Valves: Simple and effective for on/off control.
What Are Automated Industrial Valves?
Automated valves, also known as actuated valves, use actuators to open, close, or regulate valve position without the need for manual intervention. These actuators can be powered by electric motors, pneumatic pressure, or hydraulic fluid, enabling more precise and remote control over the system’s flow and operation. Automated valves are commonly integrated into automated control systems, enabling real-time adjustments based on system demands.
Types of Automated Valves Include:
Would you like to visit Indiar? A tour operator in India is the best place to plan your tour. You can book a tour from here.
- Electric Actuated Valves: Powered by electric motors, ideal for precise control.
- Pneumatic Actuated Valves: Operate using compressed air, suited for fast operation.
- Hydraulic Actuated Valves: Use hydraulic fluid to operate, offering high power for large systems.
Factors to Consider When Choosing Between Manual and Automated Valves
The choice between manual and automated valves depends on a variety of factors, including operational efficiency, cost considerations, safety requirements, and the complexity of the system. Below are the key considerations to keep in mind when making this decision:
1. Frequency of Valve Operation
One of the most important factors in valve selection is how often the valve will need to be operated. If your system requires frequent adjustments to the flow of materials, automated valves may be the better option. They can be controlled remotely or programmed to operate automatically in response to changing system conditions, making them ideal for dynamic environments where adjustments need to be made on the fly.
Manual valves, on the other hand, are more suitable for applications where the flow is steady, and changes to the system are infrequent. For instance, manual valves are often used in systems where components need to be isolated during maintenance or in emergency situations where quick shutoff is required but not on a regular basis.
Would you like to visit Haridwar? Travel agents in Haridwar are the best place to plan your trip. You can book your tour right here.
2. System Size and Complexity
The size and complexity of your industrial system also play a significant role in determining whether manual or automated valves are best. In large, complex systems that cover extensive areas—such as in oil refineries, chemical plants, or water treatment facilities—automated valves offer a clear advantage. These systems often require precise control of multiple valves simultaneously, which is far more efficiently managed through automation than by manually operating each valve.
In contrast, smaller, less complex systems may not justify the cost and complexity of automation. Manual valves can effectively meet the needs of smaller systems with fewer moving parts, where hands-on operation is sufficient.
3. Remote and Real-Time Control
One of the most significant advantages of automated valves is their ability to be controlled remotely. In industries like oil and gas, where valves may be located in remote or hazardous areas, automated systems reduce the need for human intervention, minimizing safety risks and operational downtime. Automated valves can be integrated with SCADA (Supervisory Control and Data Acquisition) systems, allowing operators to monitor and control valve operations from a central location in real time.
Manual valves, by their nature, require an operator to physically visit the site to make adjustments, which can be time-consuming and impractical, especially in large or hazardous environments. Remote control is also important in applications where real-time data monitoring is crucial, such as in chemical processing or power generation, where slight deviations in flow, pressure, or temperature must be corrected immediately.
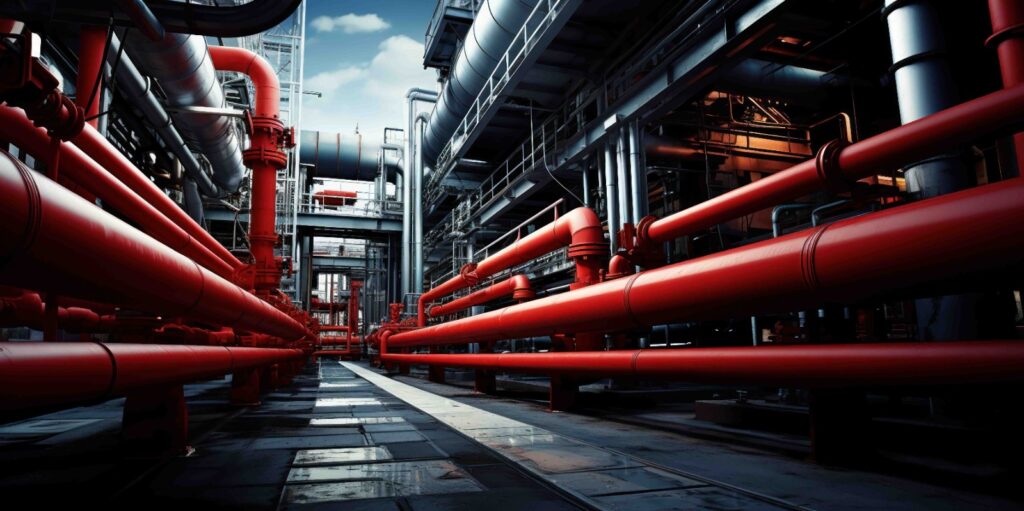
4. Safety Considerations
Safety is paramount in any industrial system, especially when dealing with hazardous materials or extreme operating conditions. Automated valves provide a higher level of safety because they can respond automatically to system changes or emergencies. For example, in the event of a system failure, an automated valve can be programmed to close or open immediately, preventing accidents, spills, or damage to equipment.
While manual valves can also serve as safety shutoffs, they rely on human intervention, which can delay the response time in an emergency. In environments where quick action is required to avoid catastrophic failure, automated valves with fail-safe mechanisms are often the better choice.
5. Budget and Cost Constraints
Cost is a critical factor in deciding between manual and automated valves. Manual valves are generally less expensive to purchase and install than automated valves, making them a more attractive option for operations with tight budgets or simpler system requirements.
Automated valves, while more expensive upfront due to the cost of actuators and control systems, can save money over time through increased efficiency and reduced labor costs. In large-scale operations, the ability to remotely control and automate flow adjustments can significantly lower operational expenses, improve productivity, and reduce maintenance costs.
6. Maintenance and Reliability
Manual valves are simpler in design and, as a result, often more durable and reliable under basic operating conditions. They typically require less maintenance because they have fewer moving parts compared to automated valves. However, this reliability can be compromised if manual valves are used in environments where frequent adjustments are necessary, as excessive use can wear out the components over time.
Automated valves, while more complex, are designed for continuous operation and can offer higher precision and consistency in flow control. However, their actuators require regular maintenance to ensure they function correctly, and automation systems need periodic calibration. Choosing automated valves often means considering the ongoing cost of maintaining the automation infrastructure, but this is typically offset by the operational efficiencies gained.
7. Energy Efficiency
Energy efficiency is another consideration, particularly in industries that prioritize sustainability or have strict energy consumption limits. Automated valves, especially pneumatic or hydraulic ones, can consume a significant amount of energy to operate, depending on the number of cycles and the actuator type. Electric actuators are generally more energy-efficient but may still require substantial power, especially for larger valves.
Manual valves do not consume energy except when physically operated, making them inherently more energy-efficient in systems with infrequent adjustments. However, the trade-off is that manual operation can be labor-intensive and time-consuming, which may offset the energy savings in some cases.
Advantages and Limitations of Manual Valves
Advantages of Manual Valves:
- Lower initial cost and simple design.
- Easy to install and maintain.
- Reliable for basic on/off applications and infrequent adjustments.
- No external power source required.
Limitations of Manual Valves:
- Not suitable for remote or hazardous locations.
- Slower response time in emergencies.
- Requires human intervention, leading to potential delays and human error.
- Not ideal for systems requiring frequent or precise adjustments.
Advantages and Limitations of Automated Valves
Advantages of Automated Valves:
- Precise control and real-time adjustments.
- Can be operated remotely, improving safety and efficiency.
- Integrated with automation systems for continuous monitoring and optimization.
- Ideal for large, complex systems or hazardous environments.
- Faster response time in emergencies, enhancing system safety.
Limitations of Automated Valves:
- Higher initial cost due to actuators and control systems.
- Requires regular maintenance of actuators and automation infrastructure.
- May consume significant energy, depending on the actuator type.
- More complex installation and setup.
Conclusion
Choosing between manual and automated valves depends on your specific system requirements, budget, and operational priorities. Manual valves offer simplicity, reliability, and cost-effectiveness in systems where frequent adjustments are not necessary, while automated valves provide precision, remote control, and enhanced safety in dynamic or large-scale operations. By considering factors like frequency of use, system size, safety needs, and long-term costs, you can make an informed decision that optimizes both performance and efficiency.